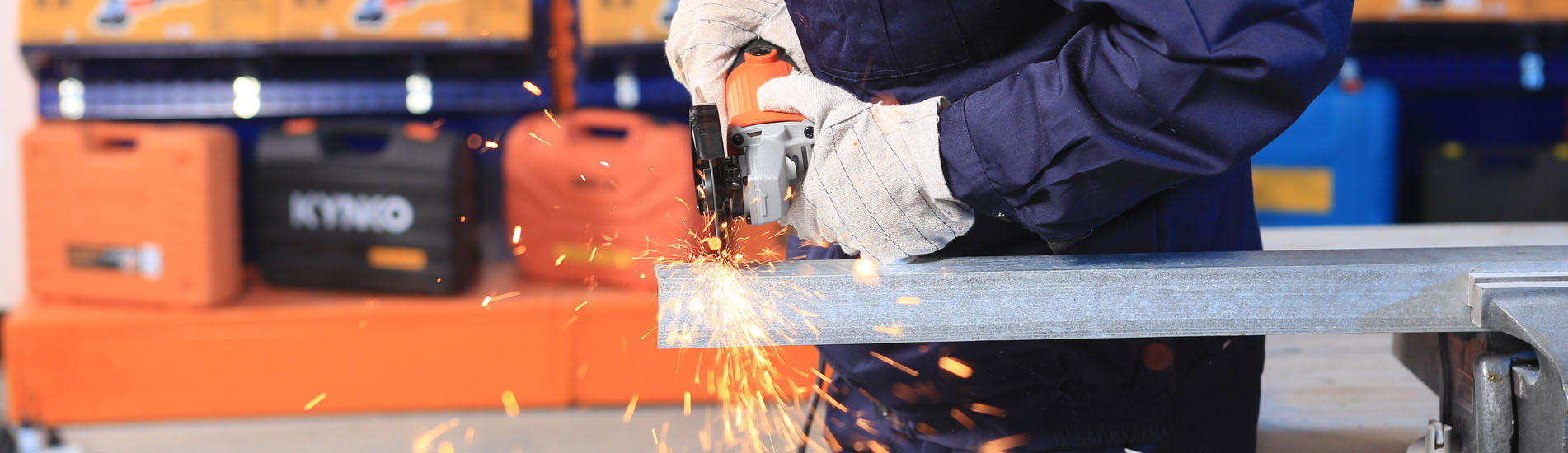
Should power tools be double insulated?
Double insulation is an important safety feature implemented in many power tools and appliances. It consists of two layers of electrical insulation instead of one to prevent electric shock.
The first layer is called basic insulation. It covers current-carrying parts and provides the primary protection against electric shock. The second layer is called supplementary insulation. It acts as a backup in case the basic insulation fails or gets damaged.
With double insulation, the user only contacts the outer layer and cannot access the live parts inside. This ensures safety even if the basic insulation fails. Double insulated tools are recognizable by the “square within a square” symbol.
Compared to Class I tools that require grounding, double insulated or Class II tools do not need a ground connection. They can be safely used without any additional protection measures. This makes them very convenient to use anywhere.
For example, the KYNKO large angle grinder has a peak power exceeding 3500W. Yet with its double insulation design, it only requires a 2-prong plug to keep the user safe. The two independent insulation barriers eliminate the need for a grounding connection, despite the high power output.
The main difference between a 3-prong and a 2-prong is the material of the tools housing. If the housing is made of conductive material, namely some iron or iron-containing compound, then the tools must have a grounding conductor and a 3-prong plug.
Double insulation eliminates the risk of electric shock without relying on grounding or a safety extra-low voltage power source. Most household and office appliances rely primarily on this insulation for user safety. That’s why safety regulations worldwide classify electrical devices based on their insulation system.
For power tools to qualify as double insulated, insulation barriers between internal components must satisfy three key criteria:
- Live parts must be separated from inaccessible metal parts by basic insulation. Live parts include rotors, armatures, brushes and exposed terminals that users cannot directly touch.
- Inaccessible metal parts must be separated from accessible ones like the housing by supplementary insulation.
- Live parts must be separated from accessible surfaces users can touch by double or reinforced insulation.
Accessible parts include the external housing, spindles, and control switches that users can easily contact during operation. If accessible parts are electrically conductive and connected to internal metal components, those also become “accessible” through that conduction path.
The insulation requirements do not imply that live parts must be completely enclosed by solid barriers. Air gaps can also provide adequate separation for insulation purposes.
Stator supplementary insulation refers to insulation layers applied over the stator windings inside electric motors. Common materials used are plastic housings, liners and barriers. There are several design approaches:
- Full plastic housing: The shell, gearbox, covers and handles are entirely plastic. This works for small power tools.
- Metal housing with full plastic liner: Used for medium-sized tools where the housing doesn't experience high mechanical loads during operation.
- Semi-plastic housing with metal insert reinforcements: Used for large heavy-duty tools that undergo axial pressures and vibrations. The metal skeleton provides mechanical rigidity while the plastic barriers provide electrical insulation.
For small tools, an all-plastic housing sufficiently insulates the stator. Medium tools often use a semi-plastic approach for better durability. Large tools designed for demanding tasks require metal structural reinforcements and thus cannot adopt an all-plastic housing; so full-plastic liners or insulation ribs are installed instead.
By insulating the stator through solid barriers or air gaps, the live internal parts become inaccessible. This supplementary insulation, combined with basic winding insulation, helps achieve double insulation for safety.
Rotor supplementary insulation refers to insulation applied over the rotor assembly inside electric motors. Common methods include:
- Insulated rotor shafts: Installing insulating layers between the rotor core and shaft. This is a simple and reliable approach used extensively.
- Insulated rotor couplings: Manufacturing the rotor shaft in two insulated segments and joining them with insulating couplers. This facilitates performance improvements.
- Insulated drive components: Insulating gears or adding insulation sleeves between shafts and gears. This is less common.
Insulated rotor shafts provide generalized protection across most tools. Insulated couplings enable better rotor designs but require positioning bearings on plastic components. Insulating drive gears necessitates plastic housings and robust grease.
By insulating the rotor and preventing external contact, supplementary barriers complement the basic winding insulation to achieve double insulation. Different tradeoffs exist between performance, design complexity and safety.
Double insulation is vital for power tool safety. When selecting tools, opt for models displaying the double insulation symbol whenever possible. All KYNKO products are with double insulation.
Categories
latest blog
Tags
© Copyright: 2003-2025 KYNKO INDUSTRIAL LIMITED All Rights Reserved.
IPv6 network supported
Talk by Wechat